CERATIZIT UK & Ireland Ltd collaborate with Volz Engineering
Estimated reading time 5 minutes
Based in Rochdale, Greater Manchester, Volz Engineering is a sub-contract machining company which services the automotive, aerospace and agricultural industries. With 6 CNC machines running 18 hours a day, Volz sends out more than 500 parts a week and there is no sign of this engineering firm slowing down the pace anytime soon!
Volz, as it is today, began its journey just over three years ago by Managing Director, Alan Reeson. What started as a manufacturing company, Volz gained its reputation by making highly precise parts to exact specifications. Eventually expanding their services to also include engineering design, Volz now oversee every step of the manufacturing process: from idea, to design, to finished product.
Having worked with CERATIZIT UK & Ireland Ltd. prior to Volz, James Alletson, Operations Manager at Volz Engineering, was keen to have CERATIZIT involved in Volz’s manufacturing processes. Regularly visited by Technical Sales Engineer, Matt Darbyshire, and Application Sales Engineer, Stuart Brooks, the engineers at Volz approach both CERATIZIT engineers with technical queries and tooling advice. Always looking to further optimize machine processes as tooling and cutting tool technology advances, the CERATIZIT engineers recommend tooling on a company-to-company basis, considering the best interests of each business above all else.
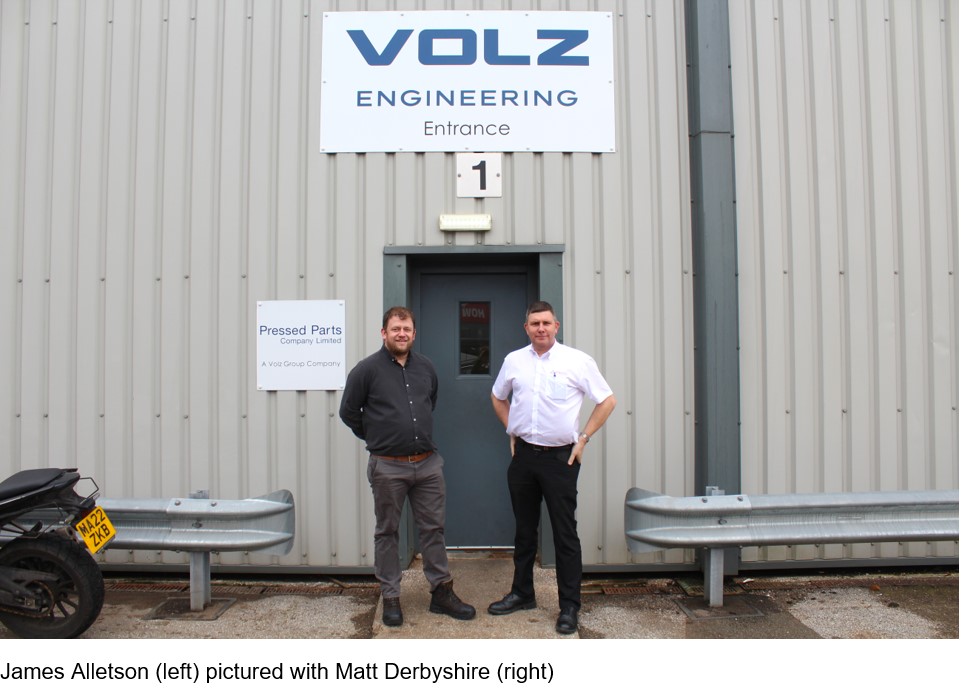
For Volz, a standout example of a tooling recommendation which had the greatest impact was for a bespoke step drill. Required for a job where one hole needed to be drilled, but with different diameters at different depths, Volz has previously been using multiple inserts to complete this job. Swapping tools throughout the process, however, meant that the overall reliability and accuracy of the finished product was reduced, and made it difficult for Volz to achieve the critical tolerance of 0.02mm. The machine process, with the necessary changes to tooling, took a total of 26 minutes. This is where Matt Darbyshire identified an opportunity to optimize this process for Volz.
Purposefully created to fulfil Volz’s exact specifications and needs, CERATIZIT designed and manufactured a totally unique step drill. After installing the drill, there were instant positive implications from switching to the step drill. The total machine process had been reduced by more than 50%, taking the time needed to drill each part to just over 10 minutes. Moreover, the step drill allowed for just one machine process to achieve the different diameters needed. So, with no machine changes or tooling swaps needed, the overall accuracy of the final products increased, allowing Volz to easily achieve the precision they required.
James Alletson commended that ‘the step drill was a game changer for us. Not only did the time taken to machine each part dramatically decrease, but with no machine interruptions we could achieve a greater level of precision. Since having the step drill delivered, we haven’t had to replace the tool yet, despite the 500 parts a week it is drilling!’
Impressed by the initial results of CERATIZIT tooling, Volz began to switch more tooling out for CERATIZIT’s products. With an increased demand for CERATIZIT tooling, a vending machine was installed on their shop floor 18 months ago and the company has continued to be impressed by the results ever since.
For Alan Reeson, Managing Director of Volz Engineering, ‘the vending machine not only means that we are never in a situation where we have to stop running machines due to lack of tooling, but it also makes it easier for us to keep track of spending. The transparency of costs through the vending machine means that exact cost of jobs are really easy to calculate, and it means that we can see just how many tools we’re using per machine.’
As well as having the machine regularly serviced and restocked, Volz have 24/7 access to technical support and advice. Regularly picking up the phone to Matt outside of his visits to Volz, the engineers have built a solid rapport with CERATIZIT that continues to benefit company.
Matt commented, ‘‘I’ve worked with Volz for a while now, and with James for even longer, so I’ve gotten to know the company and their processes really well. Having such a good working relationship with a company is important as transparency and honesty means that I can make better tooling recommendations for them. The step drill was an example where this communication and great professional relationship really helped create something extremely beneficial for the company.’
With a professional relationship that continues to grow, engineers at Volz look optimistically toward the future. Aiming to expand their repertoire of what they can offer, Volz have their sights set on achieving more aerospace certifications and accreditations which would allow them to manufacture flying parts for aircraft. Hopefully expanding the whole operation to an additional site, Alan Reeson has big plans for the company and the engineers that continue to serve the precision engineering industry well.