Mazak to debut new 3-turret high-capacity turning center at AMB
Estimated reading time 3 minutes
Yamazaki Mazak is set to unveil the latest addition to its range of high-volume turning centers at AMB 2024 with the launch of the new HQR NEO series that will offer customers increased levels of productivity, high accuracy and efficiency, all designed to dramatically boost profitability.
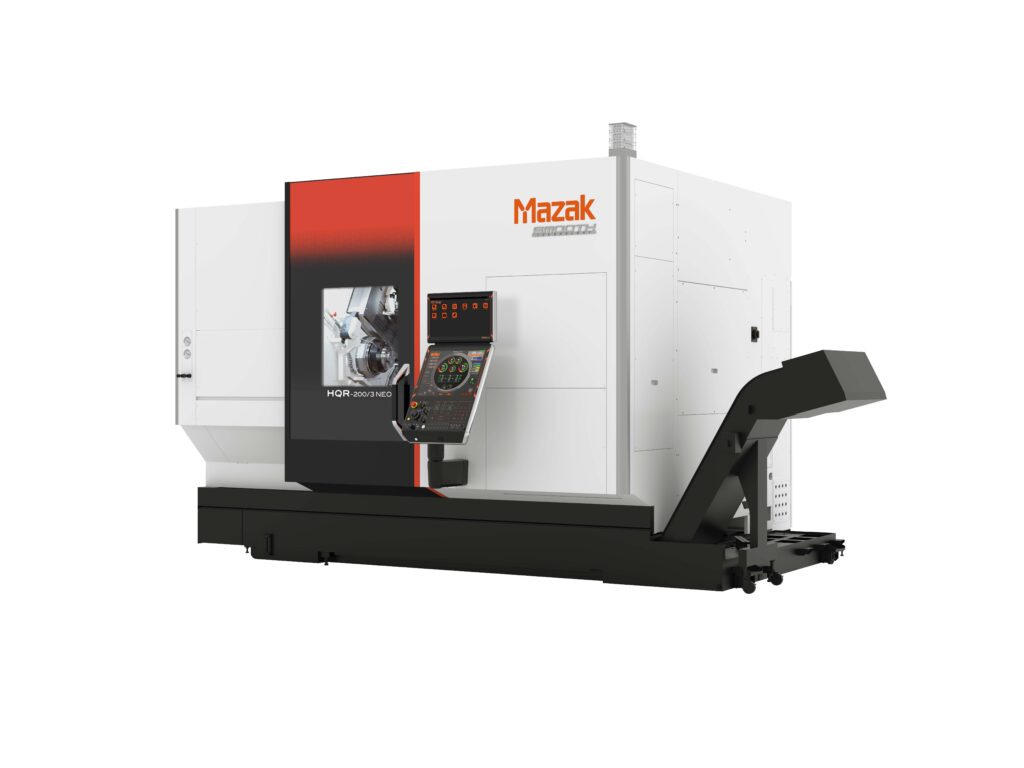
Making its world debut at IMTS in Chicago and AMB in Stuttgart is the HQR-200/3 NEO. Equipped with three turrets and two spindles, it is designed to deliver increased productivity and environmental performance.
With manufacturers striving for productivity and profitability, the additional third turret achieves a faster return on investment by reducing cycle time by approximately 25%, based on an example component produced with a two-turret configuration. The added tool stations enhance the processing capability to complete complex parts in a single set-up.
Ideally suited for medium-to-high batch sizes across the aerospace, automotive and electric vehicle, and general subcontract industries, the new machine design – which is only 120mm deeper than the two-turret version – has increased the maximum workpiece size for lower-turret chuck work from Ø212mm to Ø320mm.
The HQR-200/3 NEO on show at AMB is part of a model series comprising of two spindle sizes and three turrets. Complementing the standard 65mm and 80mm diameter bar working capability, the HQR-200/3 NEO is available with an optional enlarged Ø112mm spindle bore for bar work up to Ø102mm. Unique to Mazak, this enlarged spindle bore option facilitates the machining of prismatic components from bar material using only a turning center – work that otherwise would require a machining center to complete.
Enhanced automation features include a redesigned unloading hand that contributes to a 20% reduction in unloading time compared to previous models, while the Smooth Oscillating Cutting function automatically breaks up chips and swarf to prevent unwanted build-up for trouble-free machining.
Easy integration with automation systems is central to the design of the HQR NEO series. The new models feature an optional bar remnant disposal function to assist with the automatic operation of bar-fed components when using a short magazine bar feeder. Crucially, all automation options can be retrofitted in the field for greater flexibility.
While the addition of a third turret has resulted in a significant increase in productivity, Mazak has developed several innovations to ensure the HQR NEO series also maintains the high levels of accuracy its customers expect.
Continuous machining accuracy is stabilised by the Ai Thermal Shield function, which uses advanced algorithms to automatically determine compensation according to fluctuating temperatures, thus improving process stability for automated production.
The HQR-200/3 NEO and HQR-250/3 NEO are both controlled via the new MAZATROL SmoothG3 CNC with three channels, which uses a raft of innovative features to simplify programming, machine set-up and prove-out. The multi-channel arrangement intuitively helps operators to optimise tool paths, reduce unnecessary tool changes, balance machining time on each turret and prevent collision.
The new Synchro Editor Mode allows for easy visualisation, with all three turret programs presented side by side to enable the operator to clearly see the sequence of operations. The handwheel on the CNC control panel can also be used to manually jog through the cycle prior to full automatic operation, identifying any potential interference during the prove-out stage.
In line with the established ethos of Mazak’s NEO series, the new HQR machines benefit from noticeably improved environmental performance. Energy consumption is reduced by inverter-driven hydraulic and chiller units, while the slideway grease lubrication system has been optimised in line with the distance the machine travels. With the addition of the optional Smooth Coolant System, overall energy consumption and system maintenance is further optimised.