STARRAG’S DROOP + REIN DUO SUPERSIZES WIND POWER PRODUCTION FOR DANISH SPECIALISTS
Estimated reading time 3 minutes
Denmark-based HACO A/S has invested in two large-capacity Droop+Rein portal-type machining centres from Starrag to meet the rising demand for components for larger offshore wind power turbines having outputs of up to 16 MegaWatts.
Complementing the company’s five Dörries vertical turning and boring mills, the new machines – one focused on milling and the other as a turning machine with a third linear axis via the table – will be targeted at the complete machining of components such as rotor housings (with diameters up to 10,000 mm; though sizes up to 11,500 mm are also now being considered), as well as front and stator sheets, brake discs and other components.
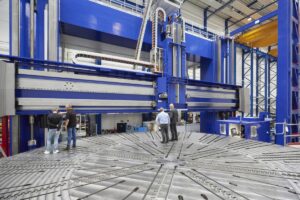
HACO’s ‘supersizing’ of its production enhances its established (60 years) contract manufacturing success, in latter years especially with the Dörries machines and on wind power components having maximum turning diameters on the flanges of 9,000 mm.
With a clearance of 12,600 mm between the portals, gantry axes travels of 14,000 mm and a stroke of 3,500 mm in the ram, the new 500 tonnes milling-based machining centre will also undertake turning and drilling of components made from high-strength welded as well as cast steel through the interaction of its 100 kW milling head with two x 111 kW master-slave main drives.
The new turning machine, with a third linear axis and an adjustable table, has similar dimensions to the milling machine but comes with an additional feature that takes into account the ever-expanding dimensions in wind power plant construction; by adjusting the table, the turning diameter can be expanded from 13,000 to 15,000 mm.
This machine is equipped with two x 136 kW master-slave main drives and a 80 kW milling head, and is predominantly designed for turning.
When it comes to wind power, Denmark is leading the way: 40% of the country’s energy requirements are fulfilled with electricity generated by wind power, and HACO’s prime customer, Valmont SM A/S, is a world leader in the supply of steel components to the wind power sector.
HACO currently processes around 10,000 tonnes of high-strength steel each year, but the wind power sector is now also increasingly looking at the use of aluminium alloys, castings and composites, so the company’s investment in the two new machines has been made with these materials also in mind.
The choice of Droop+Rein machines for this significant investment was based on HACO’s long-standing experience with Starrag on machine reliability/longevity, customer service, machine price and the delivery schedule of the new duo.
Up until now, Valmont has been transporting the welded blanks to HACO’s site 100 km away but, with this multi-year contract now embracing larger components, the two companies have decided on a more sustainable form of collaboration which sees HACO establishing a subsidiary plant for the two new machines close to Valmont’s HQ, which is near the sea.
From here, even very large and extremely heavy rotor housings can be transported via ship in a much more environmentally-friendly way, for final assembly near to the coast.