SURFACE ROUGHNESS PROBE INTRODUCED BY LK
Estimated reading time 5 minutes
Coordinate measuring machine (CMM) manufacturer LK Metrology, whose manufacturing facility is in Derbyshire, UK, has announced the introduction of the SURFACER SRP. It is a plug-and-play probe having a resolution of one micron for seamlessly analysing the roughness of the surface of a component as part of a CNC measuring cycle on any CMM, provided it has an industry-standard probe head.
The sensor eliminates the need for secondary surface roughness inspection, either manually using a hand-held instrument or automatically at a separate metrology station. Manufacturers are able to conduct comprehensive inspection on a component in a single setup in a CMM environment, resulting in significant savings in time and cost. Engineered for ease of use and versatility, the equipment comes with its own downloadable application software, facilitating integration and eliminating the need for third-party software.
Effortless swapping between touch probes, tactile scanning probes, non-contact laser scanners and the roughness probe gives users extended multi-sensor capability. The SURFACER SRP mounting is compatible with change racks, including the new versions introduced recently by LK, enabling automated sensor changing and enhanced operational efficiency.
At the heart of the roughness probe lies a special body that accommodates three interchangeable, skidded, stainless-steel probe modules. One evaluates flat, conical and cylindrical surfaces, another measures concave, convex and spherical surfaces, and a third is for inspecting grooves more than 3 mm wide by less than 10 mm deep, or steps of similar height.
The CMM positions a stylus so that it is in contact with the part, after which the machine axes remain stationary while the probe moves the stylus across the surface under investigation. Wireless communication with the CMM computer via a Bluetooth 4.0 adapter provides seamless data transfer for analysis, simplifying installation.
The skid plays a key role during measurement, acting as a straight-line datum that guides the stylus across a surface to ensure probe stability. The stylus travels independently of and slightly in front of the skid, with surface deviations recorded as the difference in the relative movements of the two elements in the Z-axis. The design ensures that even minute surface irregularities are captured with exceptional accuracy.
Further enhancing the precision of the SURFACER SRP is an integrated preload mechanism, which during stylus operation isolates it from the CMM kinematics, guaranteeing accurate and consistent results regardless of external vibration or machine movement. The force exerted by the stylus tip, which has a radius of 5 microns, is less than four thousandths of a Newton, avoiding surface deformation. Measurable roughness range is 0.5 to 6.5 Ra, which is the average roughness between the profile and the mean line.
Dave Robinson, LK’s marketing manager said, “By integrating surface roughness measurement directly onto the CMM, we are providing manufacturers with a powerful tool to streamline their inspection processes, reduce costs and enhance product quality. The ability to perform multiple metrology functions on a single platform eliminates the need for time-consuming transfers of components and ensures greater accuracy by maintaining part orientation between measurements.”
The importance of ascertaining surface roughness
Measuring the relative smoothness of the surface profile of a metal or plastic component is fundamental after turning, milling, grinding, spark erosion, broaching or reaming, as it directly correlates to how well the component will function in service. It is the small, fine-scale variations and imperfections in the surface including peaks and valleys that is assessed by LK’s SURFACER SRP, rather than larger-scale features like waviness or form.
The texture of a surface, even at a microscopic level, significantly influences its interactions with other parts and its environment. For instance, smoother surfaces minimise friction, which is vital for reducing wear of moving parts and improving efficiency, durability and performance. In applications involving seals, a precise surface finish prevents leaks. Furthermore, surface roughness can impact a component’s susceptibility to fatigue; rougher surfaces create stress points that can lead to premature failure.
Beyond mechanical functionality, the degree of surface roughness plays a role in corrosion resistance, as smoother surfaces are less prone to trapping corrosive substances. A smooth surface improves electrical conductivity. Additionally, the ability of coatings or adhesives to bond effectively is heavily reliant on surface texture.
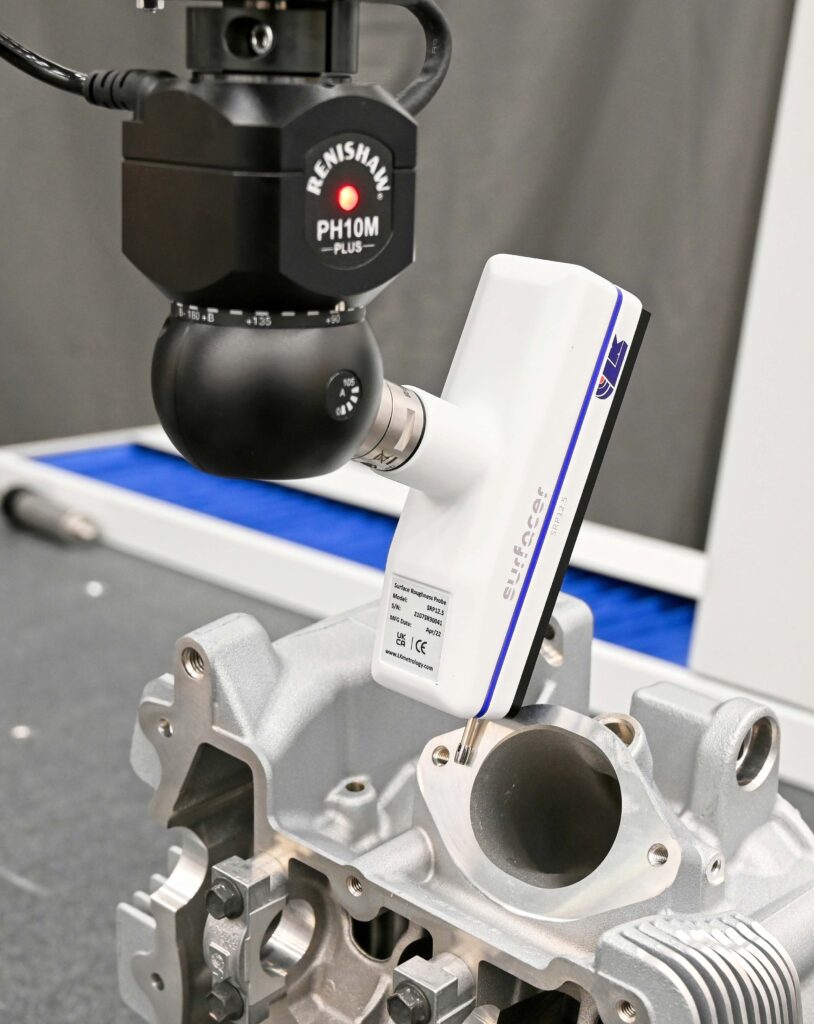
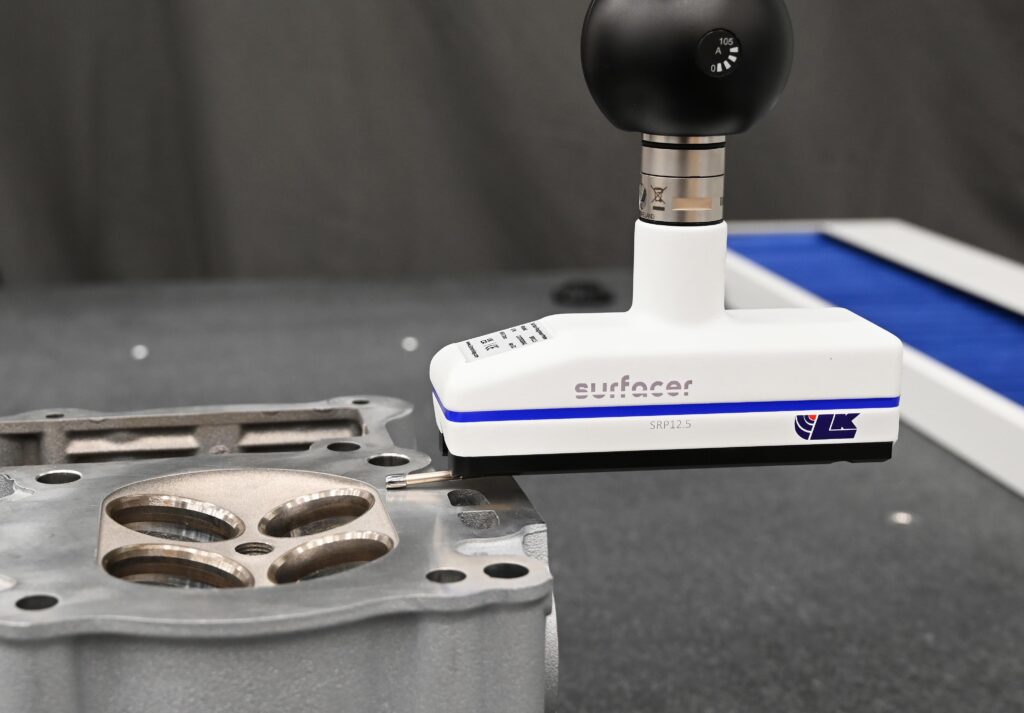
About LK Metrology
LK Metrology is renowned for innovative metrology solutions and services. The company’s products, including coordinate measuring machines (CMM), portable measuring arms and metrology software, are used worldwide to control and improve the quality of manufactured components. Its precision technology underpins the process chain from design, development, production and assembly through to quality assurance in global industries such as automotive, aerospace, defence, motorsport, energy, medical and contract inspection.
Established in England in 1963, LK Metrology has an impressive heritage in metrology dating back to the birth of CMM technology. Founded by CMM pioneer Norman Key and his father-in-law Jim Lowther, LK Metrology is credited with many of the CMM industry’s firsts including the first bridge-type design, first OEM to integrate computers, first to use a touch trigger probe, first to develop inspection software, first to use all air bearings and granite guideways, first to use carbon fibre composite spindles, first to use microprocessor-controlled drive systems, first to produce a truly thermally stable CMM and first to produce a high-accuracy horizontal-spindle CMM.
In 2018, LK Metrology was relaunched as an independent CMM manufacturer after several years as a division of Nikon Metrology. Headquartered in the UK, LK’s CMM development and production are at the company’s facility in Castle Donington. Sales and support offices are located in the UK, North America, Belgium, France, Germany, Italy and China, supplemented by a worldwide distributor network.