Powdertech Surface Science
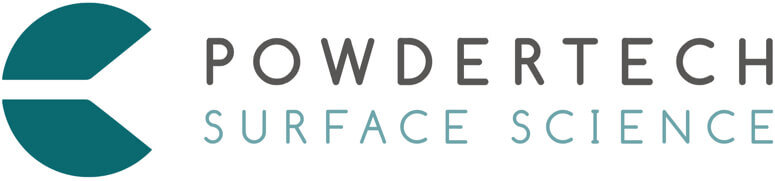
Precise, intricate powder coating is our expertise.
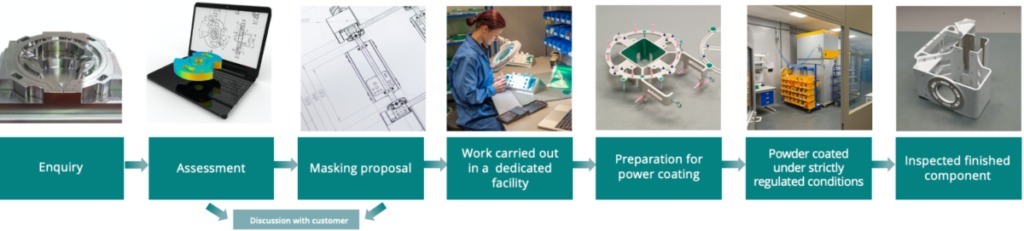
YOUR WORK IN SAFE HANDS
The ever increasing complexity and artistry of machined components in the UK has intensified the requirement for precise powder coating on advanced designs. This final stage of manufacture, the finish, seems inevitably to be under time pressure. You need your coating to be planned, executed and successfully completed to meet those tight deadlines.
Dedicated to the task
We understand these demands, and that they are growing year by year. In order to improve the service we offer and to help you meet the needs of your own customers, we have invested in a dedicated separate facility, located within our plant, to be used exclusively for handling small, complex components.
The final stage for your precision part is the precision coating. With INTRICOAT we can plan that stage with you to be ready when you are.
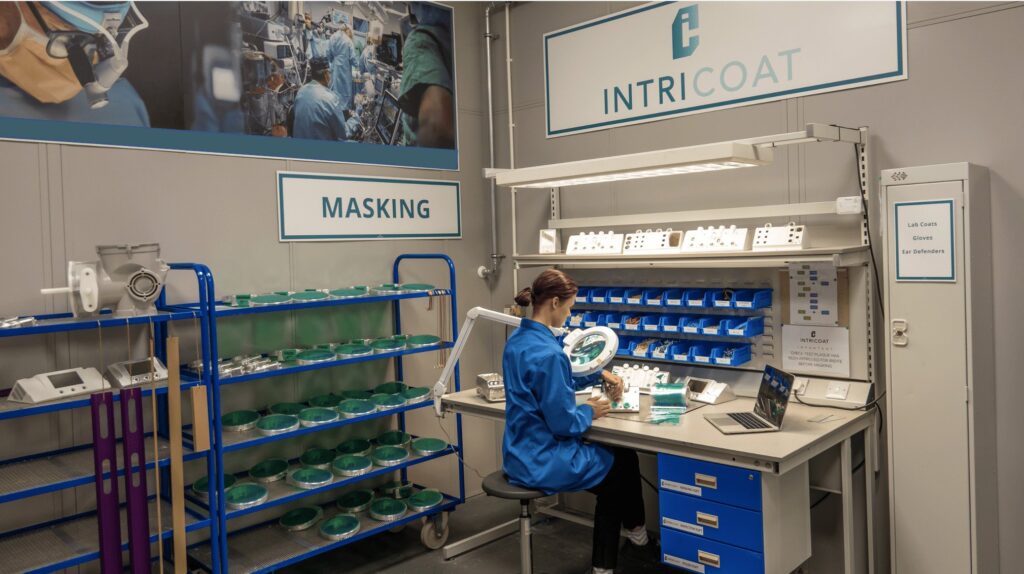
INTRICOAT – STEP BY STEP
Designing a masking scheme
Intricate components require very precise areas of surface coating, often defined by masking schemes. We can design these schemes with you to a very high degree of accuracy on a 3D CAD system, meaning that potential pitfalls can be ruled out at the design stage before any prototypes need to be made.
Coating thicknesses and tolerances will require careful measurement and monitoring. Specialist coatings and primers may be required. Every angle of every component will need to be scrutinised before it leaves our plant. INTRICOAT brings all of these disciplines together in a dedicated facility.
Benefitting from CAD
We will ask you for all available data in order to assess the powder coating requirements and minimise the need for prototype parts. With this information we will often work in 3D-CAD to help visualise the masking requirements and to understand how these relate to the rest of the component and to other connecting devices. The 3D interpretation is shared with you for confirmation and we will also explain how the powder will form over features, masks and bungs in the component. We can then design a masking scheme which will involve custom-made die-cut masking kits to prevent coverage in those areas to be left free of coating. The scheme will also indicate which masking materials need to be removed before curing and which can stay in situ. We will design your masking scheme to high such a high degree of detail and accuracy that test parts, and the time and money involved, are unnecessary.

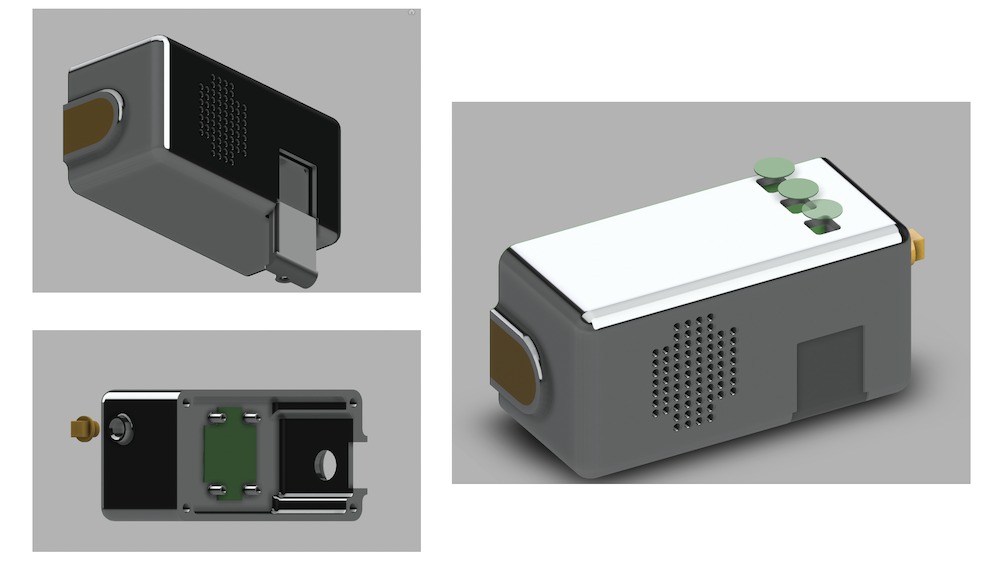
Applying masking
Using the most appropriate tape and bungs for masking is important. Tape must be of the appropriate thickness for rigidity or flexibility, whichever is needed, and resilient to the high temperatures used in the coating process. In addition to conventional masking films and bungs, INTRICOAT utilises 3D printed masks and laminated films to provide increased accuracy with masking positioning.
Masking is usually carried out after chemical pre-treatment when the part is completely dry. The masking tapes and bungs are carefully applied by hand.
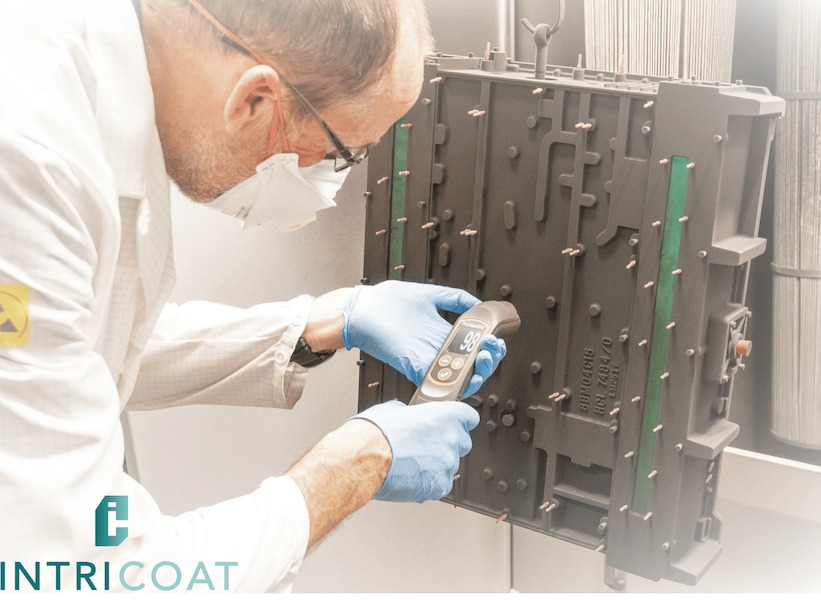
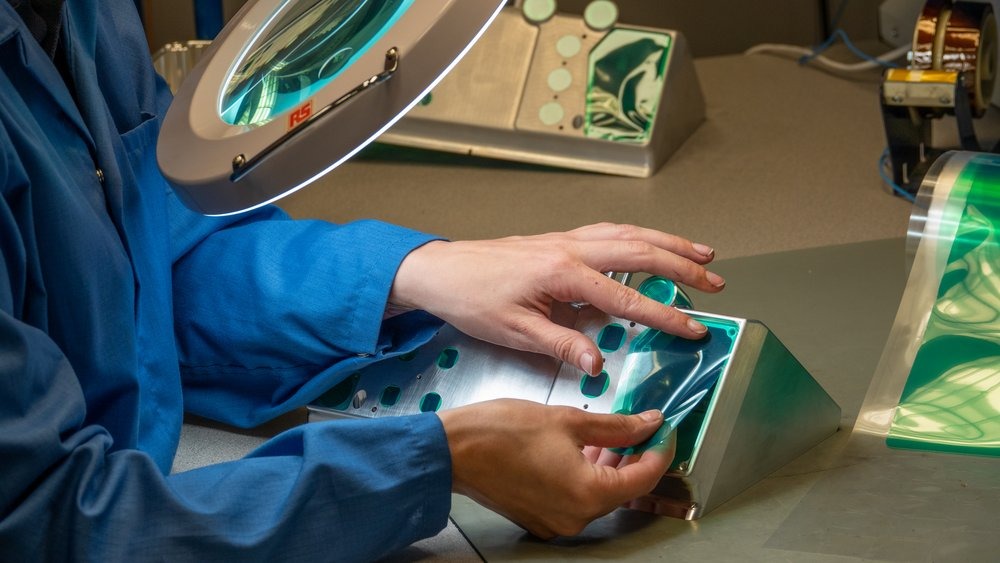
Powder coating and masking removal in stages
The parts are then powder coated and at this stage some of the masking needs to be promptly removed in aesthetically critical areas so that clean edges are retained. Knowing where and how much of the masking can be taken away is based on experience and requires some deft manipulation. Other areas of masking remain in place when the part enters the curing ovens.
Quality Control
The finished components are carefully checked for accuracy of coating and cosmetic appearance, and any special packaging requirements are implemented.
Contact Powdertech Surface Science
"*" indicates required fields