Moving manufacturing from 3D printing to injection moulding
Estimated reading time 4 minutes
3D printing has revolutionised small-scale manufacturing. Production of everything from phone holders to furniture can be made at the touch of a button and printed in anything from minutes to hours.
Whilst well suited to small-scale, low-cost manufacturing, 3D printing can become time consuming and less cost effective as production volumes increase. Plastic injection moulding can be an attractive alternative when quicker, higher quality manufacturing becomes essential.
So, what are the differences between 3D printing and injection moulding a plastic part? When should manufacturers move from 3D printing to injection moulding? And what do they need to consider when doing so?
How does 3D printing work?
3D printing is an additive manufacturing process involving printing layers of thin material (typically plastic) and fusing them together to from a part. 3D printers are used on everything from jumbo jets to prosthetic legs. It is also often the first port of call for small manufacturers attracted by the low start-up costs and ease of production.
At BEC Group 3D printing is used for prototyping, producing jigs, and reverse engineering parts in conjunction with our 3D scanner. An important benefit of the process is how rapidly design changes can be made and tested.
How does injection moulding work?
Plastic injection moulding works by injecting molten plastic into a closed metal mould tool, the plastic cools and solidifies inside the tool, taking the shape of the inside of the mould. It is then opened and ejected to reveal the finished part.
Designing and producing the mould tool is the first step of the process at BEC Group, once this has been designed and produced by a toolmaker, material selection and production runs can begin. A mould tool can be expensive to produce, depending upon part complexity. This is one of the biggest barriers to entry for smaller manufacturers.
Moving from 3D printing to injection moulding
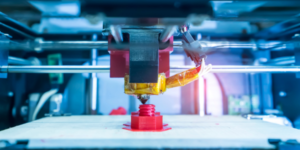
3D printing is well suited to manufacturing at low volumes – the set-up costs are low in comparison to injection moulding and can easily be produced with a home 3D printer. As production increases in volume however, 3D printing can be too time-consuming and costly. Injection moulding on the other hand is more appropriate for high volume orders which will justify the initial outlay of tooling and provide the customer with a lower cost per part than 3D printing,
For high quality, identical parts, injection moulding is superior to 3D printing. 3D printed parts are unlikely to produce identical, accurate to CAD parts. This is due to the type of printer used as tolerances can be low. 3D printed designs can be improved post-production, but often produce less polished looking parts than those injection moulded.
However, when producing parts that have frequent design changes, 3D printing tends to be a better option. Contrary to 3D printing in which designs can easily be adapted and tested almost instantaneously, changing a mould tool design is much more complex and expensive.
Design considerations
Several design considerations must be taken into account when moving from 3D printing to injection moulding. These include consistent wall thickness (to prevent sinkage and warp), adding draft angles (to allow for easy ejection of the part), the addition of ribbing (for enhancing strength).
A design for manufacture will take all of this and more into consideration to avoid further issues down the road. Reducing part complexities, rounding sharp corners, and removing undercuts will all come into play in making your part manufacturable with injection moulding.
When deciding on how to move forward with production of your part, cost, application, and production volumes should all be considered.
If you’d like to discuss moving from 3D printing to injection moulding with BEC, or a specific project get in touch via hello@becgroup.com or call us on 01425 613 131.