SSAB Ltd
SSAB are specialists when it comes to abrasion resistant and high strength steels. If you recognise the brand names of Strenx, Docol, Hardox, Armox, and Toolox; these are all a creation of SSAB. These steels have acquired a reputation for high and consistent quality, and in spite of their hardness and strength they are easy to bend, weld and machine.
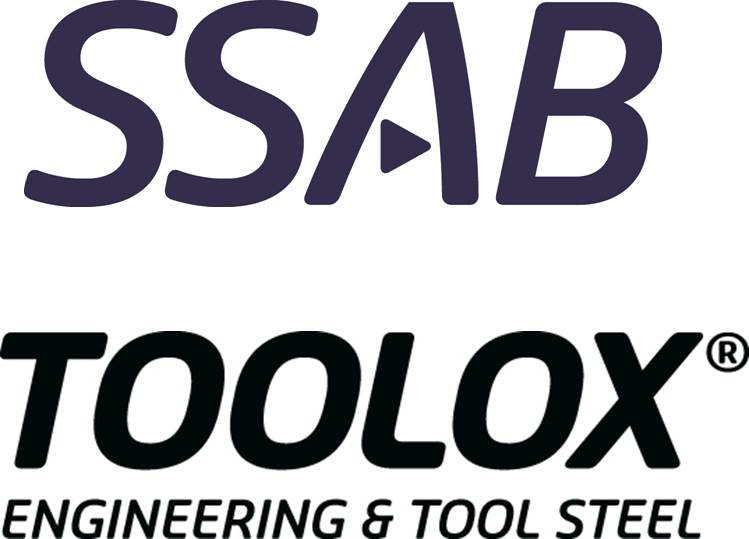

SSAB is a world leader in the specialist area of abrasion resistant and high strength steels which are marketed under the well-known brand names of Strenx, Docol, Hardox, Armox and Toolox®. These steels have acquired a reputation for high and consistent quality, and in spite of their hardness and strength they are easy to bend, weld and machine. In their heavy plate mill in Oxelösund SSAB manufacture heavy plate being quenched and tempered upon delivery from the mill.
With respect to Toolox ® engineering and tool steel, SSAB are the only steel producer in the world who manufacture material in this totally unique way compared to conventional tool and engineering steels. Therefore, exceptional properties are given to the steel using the metallurgical processes in the production line.
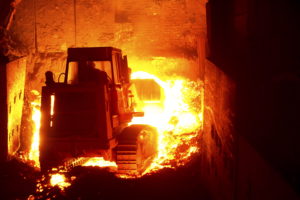
Made from pure iron ore, vacuum degassed and continuous cast (using a special process developed in Sweden called Controlled Soft Reduction) it is then rolled, quenched and tempered to meet the very exact specifications set by SSAB. Due to the high metallurgical purity, the cleanliness and very low sulphur content achieved Toolox ® corresponds to ESR quality material. Every plate is uniquely produced, and each plate is tested for hardness, toughness and homogeneity.
Toolox ® shows very low residual stresses, even after heavy machining in all grades it is dimensionally stable and normally requires no stress relieving. Which is especially useful with long thin sections such as gear racks etc. Even if machined mainly from one side the material stays extremely flat requiring no straightening and no secondary machining.
Toolox ® can be fabricated into various sections even tubes, it is very easy to weld due to the low carbon content when compared with traditional tool steels, Toolox ® will also withstand temperatures up to 590º C without any significant loss of room temperature toughness or strength. SSAB recommend a stress relieving operation after flame cutting, welding and spark erosion.
Toolox ® 33 ,300 HBW has an equal hardness to P20 (1.2311) but will machine ~40-50% faster than 1.2311.It has a typical toughness which is about 5 times higher than 1.2311. Toolox 33 also has THREE times the impact toughness of 42CrMo4 and due to the lower carbon content it is much easier to weld.
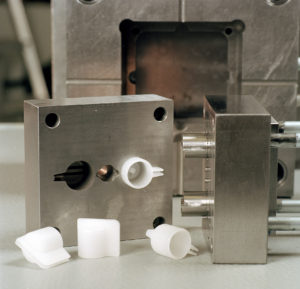
Toolox ® 44 , 450 HBW (~45 HRC) , has been developed from the company’s well reputed steel Hardox, but due to it’s unique production process it can be used as a hot application wear part up to 600C. It also has extremely high impact strength but can be readily machined and is very easy to weld. Toolox44 has up to 3 times the toughness of H13 (1.2344) at 45 HRC and up to 5 times tougher than D2 (1.2379) @ 60 HRC.
Toolox® 33 and 44 are now also available as round bars and come in a wide range of diameters from small to large. Diameters between 21 and 141 mm with lengths up to 5000 mm. Diameter ovality is in accordance to SS-EN 10060. Bright bar half of the SS – EN 10060 and impact testing in accordance to EN 10 025, EN ISO 148 with a 2 mm striker.
Toolox ® diameters are available from the local SSAB stock in Antwerp. Cut pieces of Toolox can be obtained through the well-established global network of Approved Toolox Distributors.
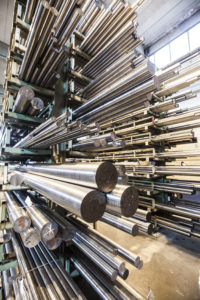
Both grades can be optically polished, nitride and PVD coated if required to tailor-make surface properties .For example a surface hardness between 60 to 65 HRC can be achieved after nitriding for very high wear resistance applications, or a coating suitable to counteract corrosive attacks, whilst still retaining a very tough core strength that is not prone to cracking or chipping.
Toolox® can be used for many applications such as:
Plastic Injection Moulding: bolsters and mould cavities, die sets
Hot Working i.e. diecasting, wear parts in hot applications, aluminium extrusion
Cold Working i.e. press tooling and forming, shear blades
Recycling knives and blades
Clamping and Holding applications, cams
Slides / Guide Rails / Gear Racks
Machine Components, bearing housings
Highly Stressed Test Rigs / Jigs and Fixtures
Just finish machine and use, no heat treatment, no stress relieving or straightening, no secondary machining. A major cost saving in manufacturing and a much quicker turn around into production with full technical back up anywhere in the world.
Carrs Toolsteel Technologies are our agent in the UK, they stock Toolox® 33 & Toolox® 44 and band saw to customer specifications. Visit them here
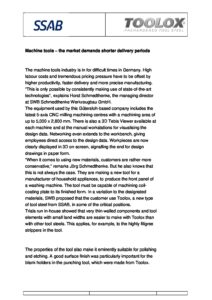
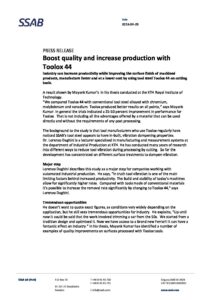
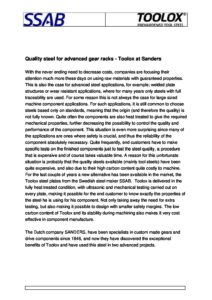
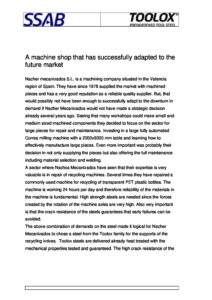
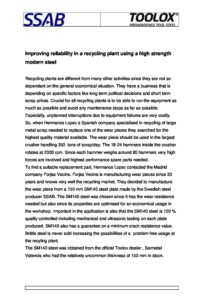
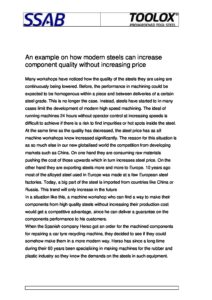
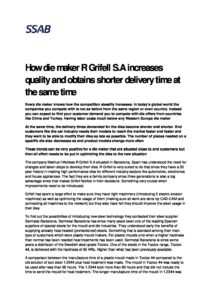
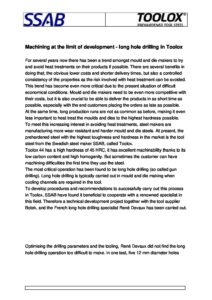
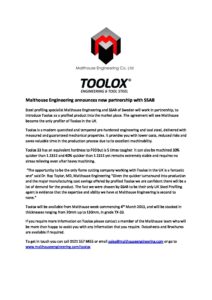
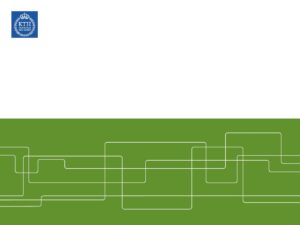
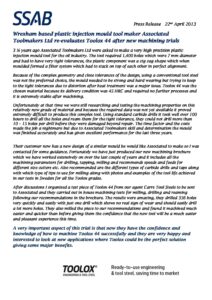
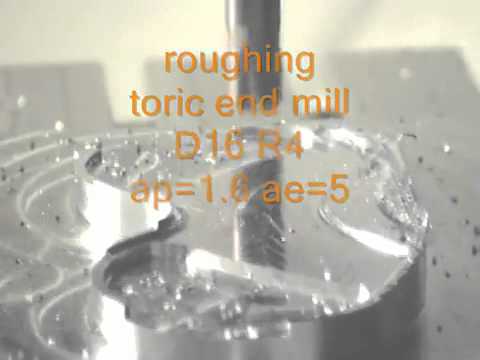
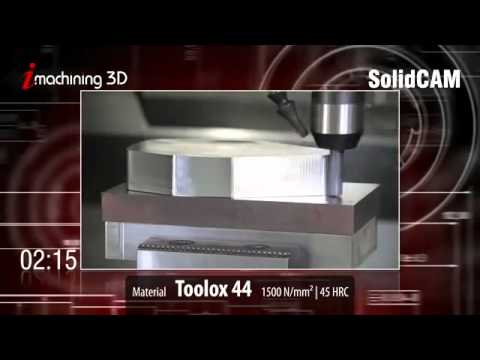
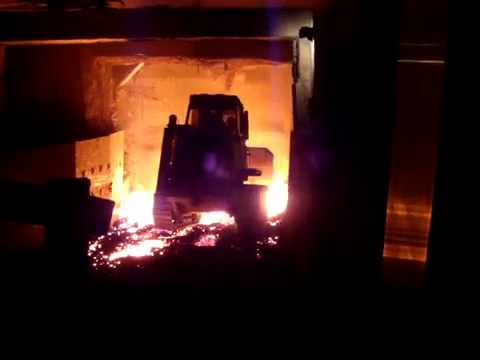

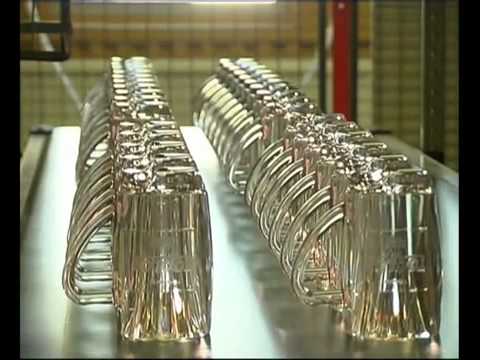
Manufacturing Resource Centre, Adams Way, Alcester, Warwickshire, B49 6PU